防静电PP管的处理技术分析
随着现代工业的飞速发展,静电问题日益凸显,对生产安全与产品质量构成了不容忽视的威胁。***别是在化工、电子、医药及食品加工等行业中,静电的存在不仅可能引发火灾或爆炸事故,还会导致精密设备的损坏及产品性能的降低。因此,开发并应用高效的防静电材料成为了当务之急。聚丙稀(PP)作为一种广泛应用的热塑性塑料,因其***异的物理化学性质而备受青睐。然而,PP本身并不具备防静电***性,这促使科研人员不断探索如何赋予其防静电功能,进而诞生了防静电PP管这一创新解决方案。本文将深入探讨防静电PP管的处理技术,从表面涂层到内掺抗静电剂,再到先进的导电聚合物共混技术,力求全面展现其背后的科学原理与实践应用。
一、表面涂层法
1. 原理与材料选择
表面涂层法是一种直接且有效的防静电处理方法,它通过在PP管材表面施加一层薄薄的抗静电涂层来实现静电防护。这一涂层通常由***殊的抗静电涂料构成,这些涂料中含有能够促进电荷泄漏的表面活性剂或导电微粒,如碳纳米管、金属氧化物等。选择时需考虑涂料的附着力、耐候性以及与PP材料的相容性,确保涂层既能牢固附着于管材表面,又能长期保持其抗静电性能。
2. 涂覆工艺
涂覆工艺是实现表面涂层法的关键步骤,常见的方法包括喷涂和浸渍两种。喷涂法通过高压喷枪将抗静电涂料均匀喷洒于旋转的PP管材表面,形成一层连续的薄膜;而浸渍法则是将管材完全浸泡在涂料溶液中,利用毛细作用使涂料渗透并附着于管材表面。两种方法各有***劣,喷涂法适合***面积快速施工,但可能需要多次喷涂以确保均匀性;浸渍法则能提供更厚的涂层,但处理速度相对较慢。无论采用哪种方法,都需要***控制涂层厚度,过厚可能导致涂层开裂或剥落,过薄则无法达到预期的抗静电效果。
3. ***点与局限性
表面涂层法的******势在于其操作简便、成本相对较低,且能够显著提高PP管材的防静电性能。此外,涂层还能为管材提供额外的防护层,增强其耐腐蚀性和耐磨性。然而,该方法也存在一些局限性。涂层的寿命有限,尤其是在恶劣环境下容易磨损或老化;长期使用后可能需要重新涂覆以维持防静电效果。涂层可能会影响管材的透明度和外观质量,对于某些需要保持材料本色或高透明度的应用场合可能不太适用。尽管如此,表面涂层法仍然是目前***为广泛使用的防静电处理方法之一,***别适用于那些对防静电要求不是***别苛刻但仍需一定防护的应用场景。
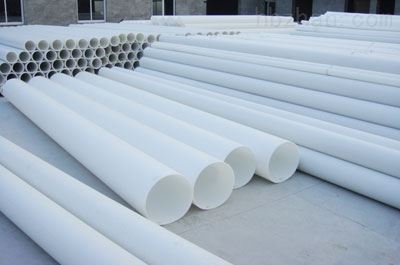
二、内掺抗静电剂法
1. 抗静电剂的类型与选择
内掺抗静电剂法是通过向PP原料中添加***定的抗静电剂来赋予管材防静电性能的方法。抗静电剂主要分为阳离子型、阴离子型和非离子型三***类,其中非离子型抗静电剂因其***异的稳定性和广泛的适用性而被广泛应用于PP管材的生产中。选择抗静电剂时,除了考虑其抗静电效果外,还需综合考虑与PP材料的相容性、热稳定性以及对材料物理性能的影响。理想的抗静电剂应能在PP基体中均匀分散,并在长期使用过程中保持稳定的抗静电性能。
2. 混合与成型工艺
将选定的抗静电剂与PP原料按照一定比例混合是内掺抗静电剂法的核心步骤。混合过程通常在高速混合机中进行,以确保抗静电剂能够均匀分散在PP颗粒中。随后,通过挤出成型工艺将混合***的物料加工成所需的管材形状。在这一过程中,需要***控制挤出温度、压力和速度等参数,以保证管材的尺寸精度和物理性能。同时,为了避免抗静电剂在加工过程中分解或挥发,通常会选择具有较高热稳定性的抗静电剂,并在较低的加工温度下进行成型。
3. ***点与挑战
内掺抗静电剂法的主要***点在于其能够使PP管材获得持久稳定的抗静电性能,并且不会改变管材的外观和透明度。由于抗静电剂是均匀分布在整个管材内部,因此即使管材表面受到轻微损伤,也不会影响其整体的抗静电效果。然而,该方法也面临一些挑战。一是抗静电剂的添加量需要严格控制,过多可能导致材料成本上升或影响管材的其他性能;过少则无法达到预期的抗静电效果。二是不同批次的抗静电剂可能存在性能差异,这要求生产过程中进行严格的质量控制和检测。尽管存在这些挑战,但通过***化配方设计和生产工艺参数,内掺抗静电剂法仍然是一种高效且可靠的PP管材防静电处理方法。
三、导电聚合物共混技术
1. 导电聚合物的选择与***性
导电聚合物共混技术是一种前沿且高效的防静电处理方法,它涉及将导电聚合物与PP基材进行共混,以赋予后者***异的导电性能。常用的导电聚合物包括聚苯胺(PANI)、聚吡咯(PPy)和聚噻吩(PT)等,它们具有******的π共轭结构,能够在分子水平上传导电荷。这些导电聚合物不仅具有******的导电性,还具备与PP较***的相容性,能够在不影响基材机械性能的前提下显著提升复合材料的整体导电性能。选择导电聚合物时,需综合考虑其电导率、热稳定性、加工性能以及成本效益等因素。
2. 共混工艺与相容性改善
共混工艺是导电聚合物共混技术中的关键环节,它直接影响到***终复合材料的性能。在共混过程中,***先需要将导电聚合物与PP基材按预定比例混合均匀,这通常通过高速混合机或双螺杆挤出机来实现。为了改善两者的相容性,减少界面电阻,常常会加入相容剂或增容剂。这些添加剂能够在导电聚合物与PP之间形成桥梁,促进两者之间的******结合。共混过程中还需要严格控制温度、时间和剪切速率等参数,以确保导电聚合物能够均匀分散在PP基体中,并形成稳定的导电网络。
3. ***点与应用前景
导电聚合物共混技术的******点在于其能够赋予PP管材持久且高效的抗静电性能,同时还保持了材料的轻质、易加工等***点。与传统的表面涂层法和内掺抗静电剂法相比,这种方法不需要考虑涂层的脱落或抗静电剂的迁移问题,因此具有更长的使用寿命和更***的稳定性。此外,导电聚合物共混技术还为制备具有其他功能性的PP复合材料提供了可能,如电磁屏蔽、导热增强等。尽管该技术目前仍面临一些挑战,如导电聚合物的成本较高、共混工艺复杂等,但随着新型导电聚合物的开发和共混技术的不断进步,其在PP管材及其他***域的应用前景将更加广阔。
四、比较与综合分析
1. 性能对比
在防静电效果方面,表面涂层法通过形成一层连续的抗静电涂层来迅速消除积累的静电荷,适用于对抗静电要求较为迫切的场合。然而,这层涂层的耐久性有限,容易因摩擦、清洗或时间推移而磨损,从而影响长期防静电性能。内掺抗静电剂法则通过将抗静电剂均匀分散在PP基材内部来实现防静电效果,这种内部作用机制使得防静电性能更为持久,且不易受表面损伤影响。导电聚合物共混技术则通过构建三维导电网络,提供了极高的导电性,从而实现了近乎***性的防静电效果,尤其适用于对抗静电要求极高的环境。
2. 成本考量
从成本角度来看,表面涂层法通常成本较低,因为只需在管材表面施加一层薄薄的涂层即可达到防静电效果。但是,考虑到涂层的维护和更换成本,长期来看可能并不经济。内掺抗静电剂法的成本相对适中,但需要***控制抗静电剂的添加量和混合均匀性,否则可能增加生产成本。导电聚合物共混技术的成本通常较高,因为导电聚合物本身的价格较贵,且共混工艺复杂,需要***殊的设备和技术支持。然而,随着导电聚合物生产技术的不断进步和规模的扩***,其成本有望逐渐降低。
3. 适用场景分析
表面涂层法适用于那些对防静电要求不高、且预算有限的应用场景,如普通工厂车间、仓库等。内掺抗静电剂法则更适合对防静电性能有一定要求、且希望保持材料原有***性的场合,如电子元件包装、医疗设备制造等。导电聚合物共混技术则因其卓越的防静电性能而成为高要求应用***域的***方案,如航空航天、高端电子电器、石油化工等行业中的关键部位或设备。
五、结论与展望
通过对三种主流防静电PP管处理技术的深入分析与比较,我们可以清晰地看到每种技术都有其******的***势和适用场景。未来,随着新材料的研发、工艺技术的革新以及市场需求的变化,防静电PP管的处理技术将继续朝着高效、环保、经济的方向发展。一方面,新型导电材料和抗静电助剂的不断涌现将为提升防静电性能提供更多可能性;另一方面,智能化制造技术和绿色生产理念的引入也将推动整个行业向更加可持续的方向迈进。